Within today's fast-paced business environment, the demand for groundbreaking solutions is higher than ever. Businesses are continuously seeking ways to bring their ideas to life efficiently and efficiently. One of the key disruptive approaches gaining traction in the realm of product manufacturing is fast injection molding. This cutting-edge technology not only accelerates the production process but also improves design flexibility, allowing companies to stay ahead of the competition.
Rapid injection molding streamlines the transition from idea to final product, reducing production times significantly. By employing advanced techniques and resources, manufacturers can produce high-quality prototypes and production parts faster than traditional methods. This efficiency enables designers and engineers to test and refine their ideas swiftly, resulting in products that fulfill customer needs and requirements with accuracy.
Understanding Fast Injection Forming
Accelerated molding molding is an sophisticated creating technique developed to accelerate the production of synthetic pieces. This technique facilitates for the rapid production of molds, employing various methods like three-dimensional modeling or CNC machining. By greatly reducing the lead time related to typical injection molding, manufacturers can adapt promptly to market needs and bring products to reality more efficiently.
One of the fundamental benefits of accelerated injection forming is its power to allow quick modeling. Developers can swiftly try out and revise their concepts, permitting on-the-fly modifications to boost functionality or appearance. This repetitive process enables organizations to enhance their product designs before committing to full-scale manufacturing, minimizing the risk of costly changes afterwards.
In furthermore quicker production cycles, accelerated injecting forming offers adaptability in development. Whether it’s detailed forms or tailored resources, this method can accommodate a wide range of specifications. As a outcome, organizations can produce customized answers designed for varied client needs, boosting their competitiveness in an ever-evolving marketplace.
Advantages of Rapid Injection Manufacturing
Fast injection molding offers substantial speed benefits over traditional manufacturing techniques. With the ability to produce molds in a fraction of the duration, businesses can transition from development to production in less time. This fast-track method allows businesses to react to market demands swiftly, reducing the period needed for launching products and allowing for faster revisions based on user input. As a consequence, businesses can remain competitive and innovative by launching products to market in unprecedented time.
Affordability is another compelling advantage of fast injection molding. By employing innovative techniques and tools, producers can minimize waste and optimize material usage, leading to lower overall production costs. Moreover, because the forms can be created quickly and at reduced initial costs compared to conventional approaches, businesses can save on costs associated with extended intervals and large upfront investment. This feature allows even small enterprises to access high-quality manufacturing without breaking the bank.
Finally, rapid injection molding improves product standards through precise and consistent production. The advanced tools used in the process allows for strict specifications and great degrees of detail, resulting in exceptional finished goods. This uniformity ensures that products not only fulfill but often surpass client demands. Furthermore, the capacity to quickly create samples and evaluate various designs encourages innovation, making it possible for producers to refine their items with minimal risk and cost.
Implementations in Product Development
Speedy molding has transformed the way product design and brought to market. One of the most notable applications is in the creation of goods for consumers where speed and adaptability are crucial. Using rapid molding, designers can create prototypes quickly, allowing for iterative testing and feedback. This quick cycle not only speeds up the design process but also enhances teamwork among teams, resulting in items that more effectively meet the needs of consumers.
In the auto sector, rapid injection molding is instrumental in creating parts such as dashboards and interior fittings. The capability to produce high-quality parts at a much faster rate enables manufacturers to react to market shifts and tech developments more effectively. This flexibility is important in a very competitive industry where setbacks can lead to lost opportunities and increased costs. Fast molding also enables more complex shapes, which can lead to innovative designs that were previously challenging to achieve.
Healthcare design is another area where speedy molding has made a considerable difference. With strict regulatory requirements and a need for accuracy, the speed of speedy molding enables the creation of models and manufacturing batches required for testing and approval. This ensures that critical healthcare items can be introduced to the market quickly while still adhering to safety and quality standards. In conclusion, rapid molding not only streamlines the design process but also empowers sectors to advance creativity.
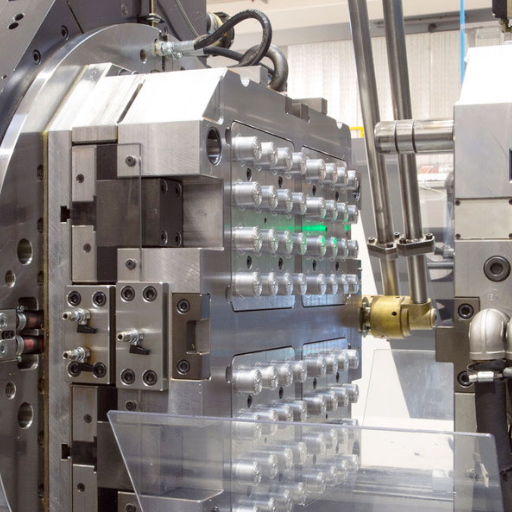